The effects of silicosis in the stone industry is not an unknown issue.
But to what extent are stone workers aware of this issue? Are the specific causes of silicosis in the stone industry common knowledge?
A scientific report from nature.com highlights the difference between engineered stone and natural stone, in relation to their silica content, shedding some light on where the cause of silicosis could lie in the stone industry.
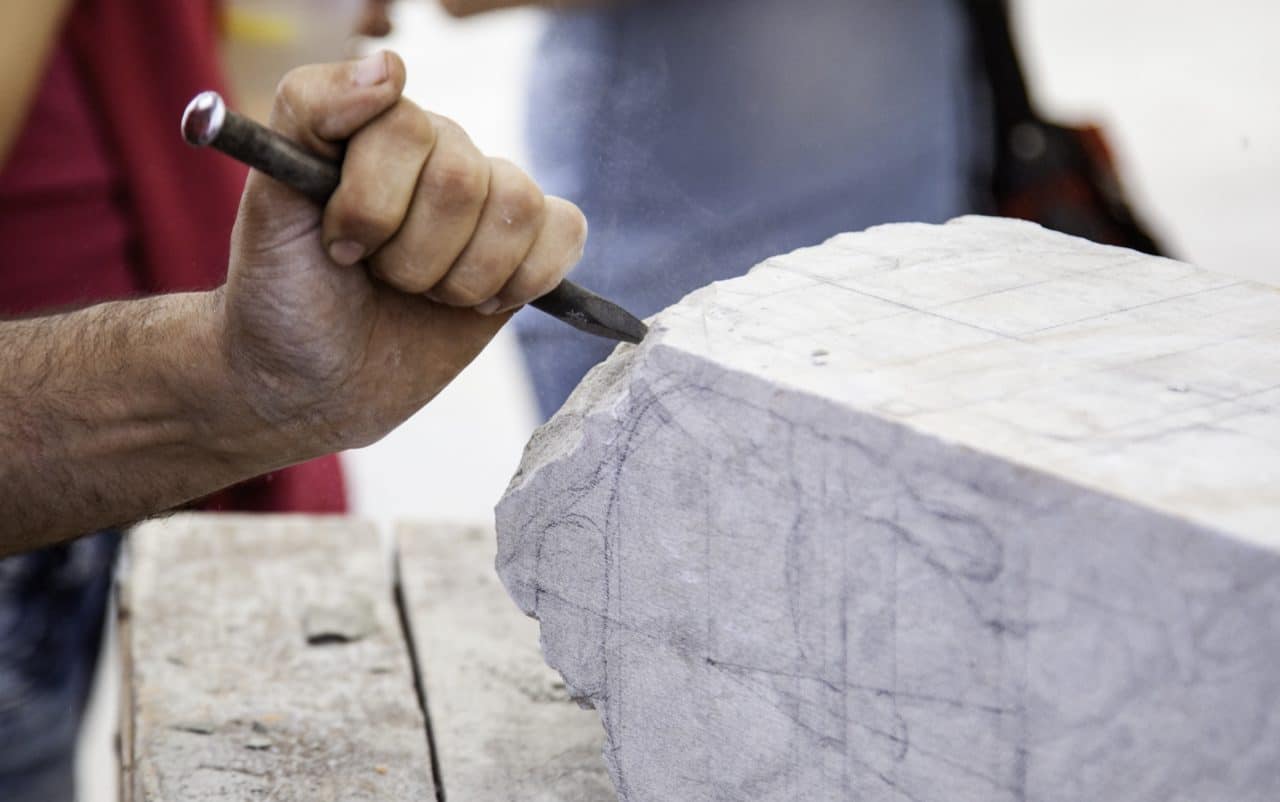
Silica dust is causing life-changing problems for stone masons
Silicosis is one of the most dangerous respirable lung diseases in the workplace, especially when exposure to harmful silica dust is a common occurrence, such as in the stone industry.
It is estimated that globally, 40 to 50 million workers are exposed to silica dust in the workplace.
The Natural Stone Institute guide to awareness and prevention of silicosis determines that exposure to respirable crystalline silica (RCS), specifically in the stone industry comes from cutting or grinding materials, most commonly which contain quartz, is composed of silica dust.
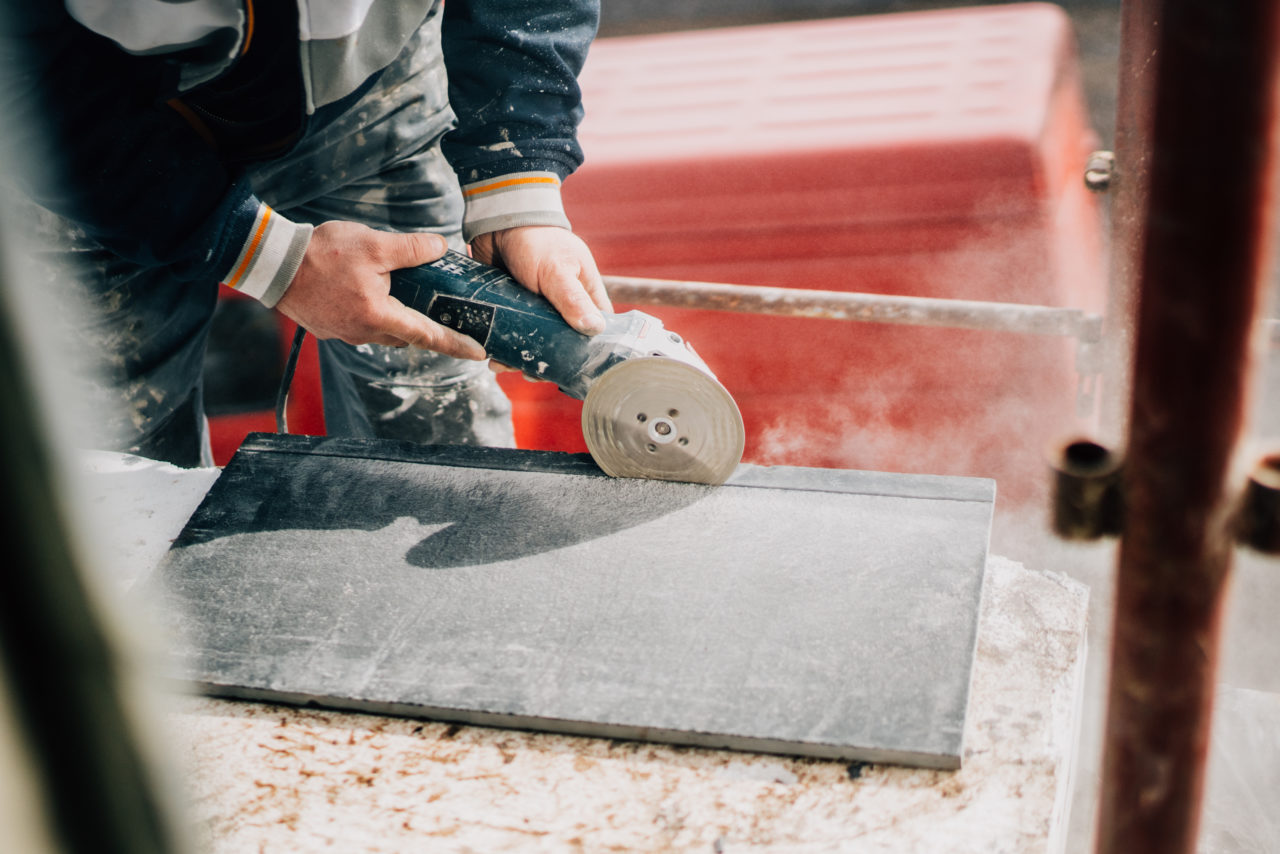
Engineered stone vs Natural stone
The purpose of the study from nature.com was to see, in relation to RCS, what the most threatening scenario was for worker’s health, in real time, when working with different compositions of stone.
In the study, 12 engineered stones were assessed against three natural stones – white marble, white granites and black granites. By dry-cutting all stones, silica dust was captured in a closed environment and subjected to various assays to determine both chemical and physical properties.
The 12 engineered stones’ silica content varied from one another, and the total RCS content made up of quartz and cristobalite ranged from 70.4% to 90.9%. By comparison, the natural stone’s silica content ranged from 3.5% to 30.1%, marking a clear difference.
As well as this, the dry-cutting of engineered stone generated finer RCS particles with one engineered stone having an average size of as little as 190 nanometres, meaning it could reach deeper in the lungs, in turn causing more damage. Contrastingly, the smallest average particle size of the natural stone was black granite, with an average size of 503 nanometres.
The results of this study concluded that silica dust emissions from engineered stones had a much higher concentration of quartz and cristobalite, therefore having a higher silica content and subsequently more damaging impact on respiratory health.
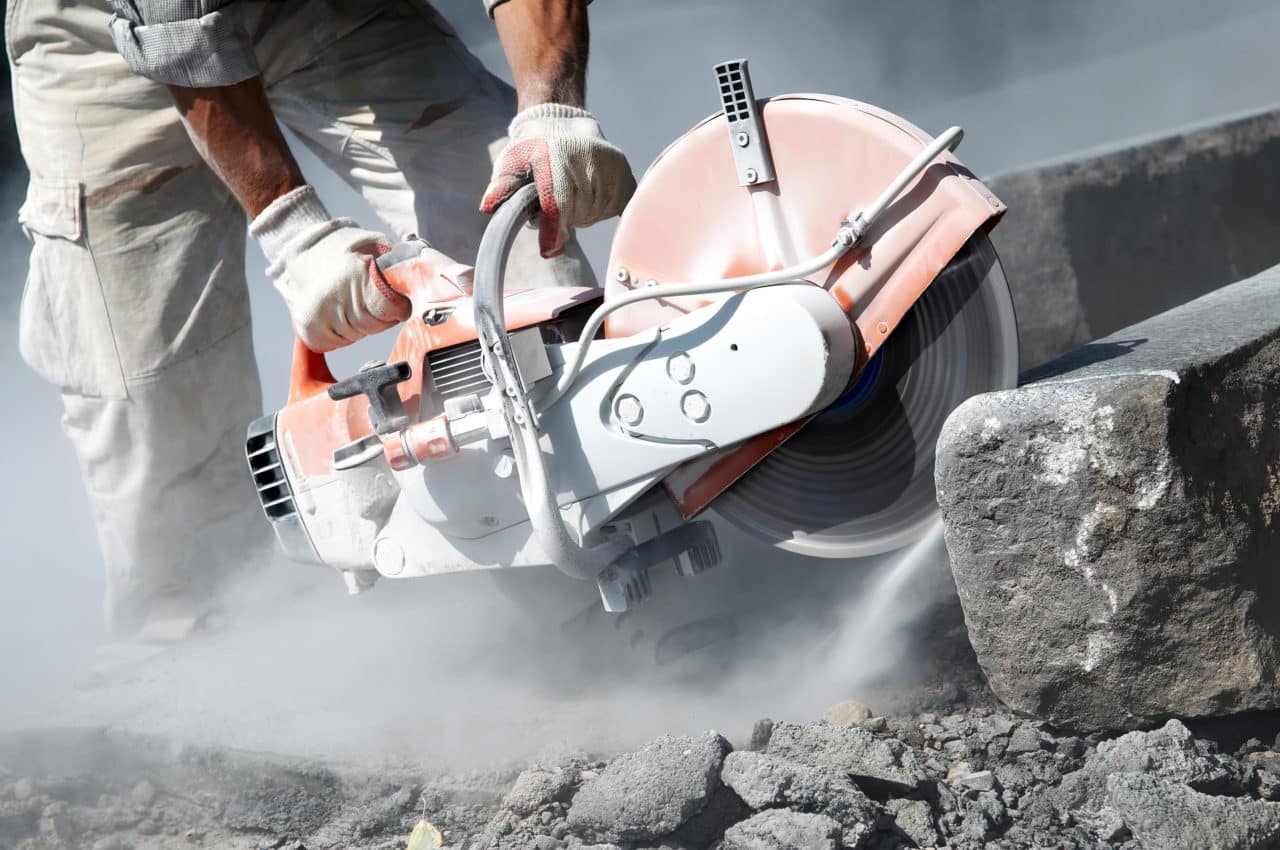
Is there a solution to silicosis within the stone industry?
Ultimately, the report concluded that the higher the silica content of the stone, as well as the smaller size of RCS particles, the more dangerous it is to respirable health.
The Natural Stone Institute conclude in their guide to occupational silicosis that there is no cure for silicosis; however, “with the proper equipment, training, vigilance and continual monitoring, you and your shop floor can be free of the dangers”.
Being aware that harmful silica dust is higher within engineered stone, compared to natural stone, and by monitoring for this, as well as using correct respirable protective equipment (RPE) when working with engineered stone, it allows for correct precautions to be taken to avoid silicosis.
Prevention is the best cure.
We’ve developed the world’s first real-time silica monitor, the AIR XS Silica Monitor, and, along with other health and safety controls, this is one of the tools that will help to prevent occupational silicosis for those exposed to harmful silica dust in the workplace.